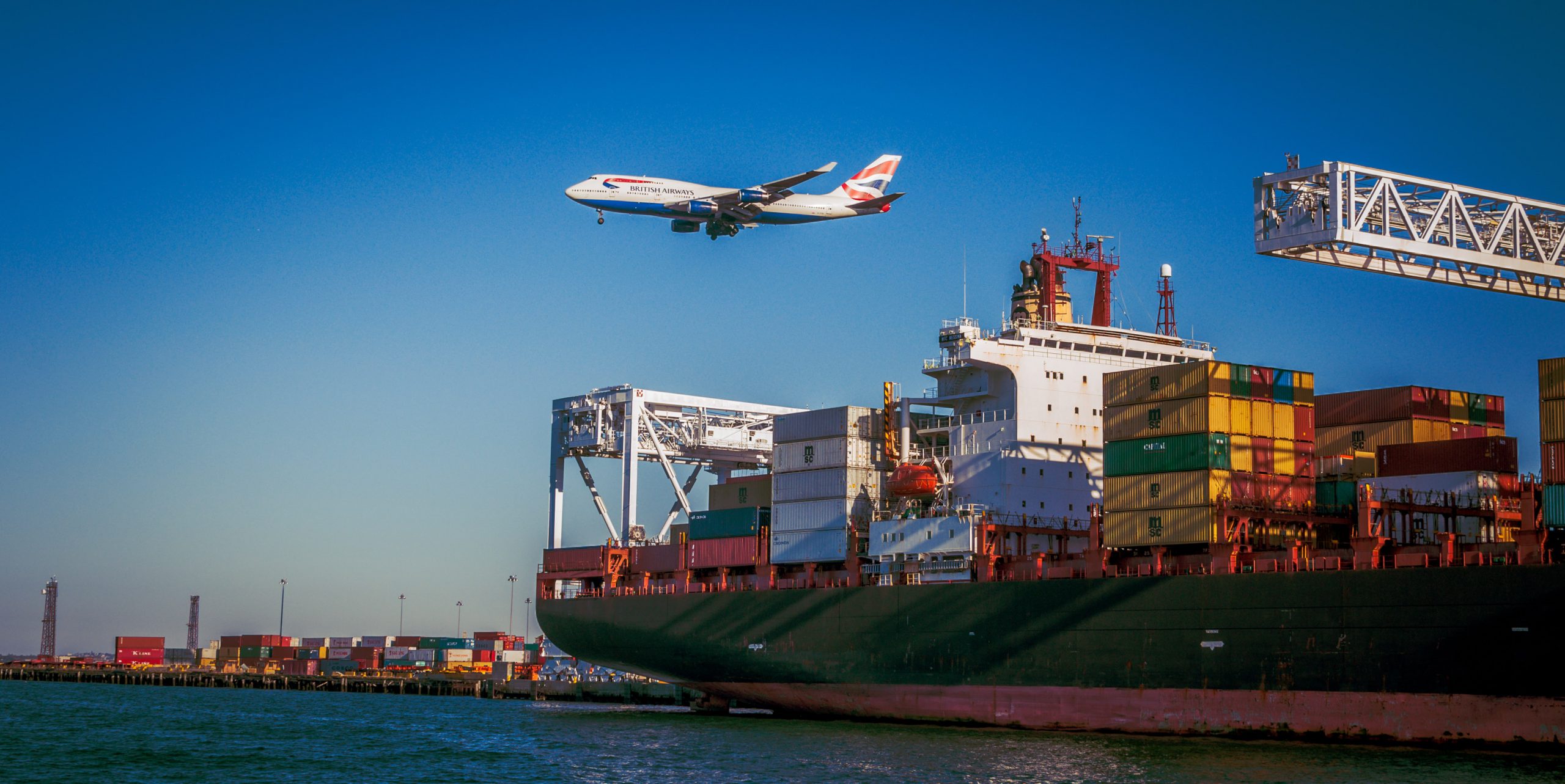
Common shipping handling and freight challenges faced when delivering physical products
If you're in the industrial shipping game, you'll know that there are two challenges your business often faces. The first is how to keep costs down to ensure you make a good margin. The other is how to deal with crises that could put your contracts with customers at risk. Here we look at three common questions and issues and discuss how you can solve them.
How can I prevent weather-related shipping disasters?
Your aim is to deliver a package to a customer safely and on time. You can’t control the weather, but you can take steps to ensure you keep to your side of the bargain. Weather predictions are pretty accurate these days, so your logistics department should be primed to keep an eye on the forecast, as well as any transport delays that they anticipate. You can assume that certain periods will be more risky for shipping, such as winter. Plan for these by letting your customers know that at these times of the year, delays can be expected. They should adjust their delivery times if possible to accommodate this.
Communication with your customers is key. If you have any concerns that their delivery may be delayed, or damaged, keep them updated on the status of the shipment. If they know what to expect, they can make plans to accommodate the late delivery or damaged item. It wouldn't hurt to offer them a discount or some form of added value to help ease their frustration. Of course, if you are thorough with your packaging and don't cut corners, you can cut down the risk of damage. This is where using pallets instead of individual boxes can give you the edge on your competitors.
Other steps you can take to protect inventory include:
? Using the correct size container and filler to protect goods
? Don’t overfill loads, or underfill them
? Ensure all pallets are regular in shape and not loose
? Use the correct stretch wrapping for the product you are shipping
? Custom package goods that are fragile or heavy
Will custom packaging save my company money?
If you run a successful business, it's partly because you've invested in the appropriate software or automation to make your packaging process streamlined and waste-free. If not, a custom packaging solution for your company will give you these benefits.
? A custom packaging design can help prevent accidents and work-related injuries in
manufacturing and warehousing. Not only do these injuries make life hard for employees and impact on their ability to work, but it also puts pressure on you as an employer financially and practically if they are off work.
? A custom packaging solution will improve both productivity and efficiency. It could mean there are fewer steps in the packaging process they will have to perform by hand. Speeding up their work by simplifying it will pay off for everyone.
? When you select custom packaging materials, remember that the cheapest material won't always help you save on packaging. It may mean you have to cough up more for filler.
? Keep sustainability in mind. Switch to recyclable and reusable systems where you can to reduce your carbon footprint. They can decrease your costs if you find the right solution. There are innovations in this area all the time. You may never have considered investing in reusable materials such as pallets. They could improve the service you offer customers by reducing damage to goods and cut your costs because you can pack more product, more efficiently.
How can I cut down on my packaging costs?
There are no one-size-fits-all solutions for packaging. However, here are some of the ways you can trim costs.
? Look into reusable material. If you ship products between facilities, this is an option for you. If you’re using wooden boxes, they may not last more than a few trips, however. It makes sense to invest in a container that is made of durable material so it can be used in the long term.
? When you are in the situation that you have to ship different sized boxes, it's unlikely they will all weigh the same. Investing in weight counting will save your staff considerable time, and therefore reduce your labour costs.
? Preventing damage to the product should be your top priority. If an item is damaged because you cut back on material, you'll likely lose the customer.
? If you have been using the same supplier for some time, try to go back to them to renegotiate terms and see if there is a newer or more affordable solution they can offer you. Also, ask them to reconsider their prices. If you're a good customer, they may be willing to reward you for this. Take this route before you decide to dump them and look for a new supplier. A good relationship and a reliable supplier are as important as the price.
Melbourne packaging supplies has been providing packaging solutions for more than 4 decades.
Author Bio: Phil Edwards is an Outreach Specialist for Melbourne Packaging Supplies. Our goal is as with quality comes reliability & safety. For more information visit
melbpack.com.au